When analyzing a phosphate, it’s important to take into account 2 types of parameters :
- Nutritional parameters which will be useful to evaluate the quality of the product ;
- Technological parameters which give information about the stability of the product and therefore the chemical reaction risk.
This article is a review of the technological parameters and their characteristics which are important to take into account when formulating animal feed and when switching from a feed phosphate to another.
Granulometry
Granulometry corresponds to the determination of the dimensions of a material (particles/ powder / grains / split solids) and more precisely its respective percentages with the study of size distribution. Granulometric analysis is therefore the set of operations whose aim is to determine the granulometric distribution of the elements making up a sample. This method is frequently used in the food industry, fine chemicals, additive manufacturing and pharmaceutical industries.
There are various methods for determining particle size. The choice between the different existing methods depends on the particle size. While large particles are measured by hand, particles > 10 µm of diameter are often measured with sieving and those < 10 µm diameter with laser diffraction or dynamic light scattering : when the laser beam penetrates the sample, the small particles scatter the light widely, while the large particles scatter the light at small angles. This method, which incorporates image analysis, is widely used because it is reproducible, reliable and at reasonable cost. The Coulter counter is another method based on the variations in electrical resistance induced by particles as they pass through an orifice immersed in an electrolyte. Finally, when it is not possible to access a laboratory or take away samples, sedimentation which is based on the relationship between the velocity at which particles fall in a fluid and the radius of the particles, can be used.
Granulometry can be determined either dry or wet. The dry method is used to characterise powders without destroying the initial aggregation. The liquid route is used to disperse the particles. The analysis will be carried out on particles in suspension.
Granulometry can impact other technological parameters of feed phosphates. Its uniformity can indeed influence the homogeneity of the final product. Flowability, caking risk and reactivity can also be impacted by the particle size : the risks are higher when the particles are smaller. The production and the facilities’ characteristics should be taken into consideration when choosing the most suitable particle size.
Each Phosphea’s product has a specific granulometry (granular, micro-granular or powder), each granulometry corresponding to a specific sizes range as showed in the tab below.
Granular | 0.5 to 2 mm |
Micro granular | 0.2 to 1.8 mm |
Powder | 0 to 0.25 mm |
Flowability
The flowability is the ability of a powder to flow freely in a smooth and constant manner in the form of individual particles.
If the powder is “hard to flow”, it may form clumps that can damage the machinery. The best and thus desired flowability value is 100.
Flowability can be influenced by intrinsic parameters such as water content and particle size, but also by extrinsic parameters such as humidity and temperature.
The main existing methods to measure the flowability of powders are the followings:
- The method of the angle of repose measures the angle formed by a powder when it is poured into a heap. A smaller angle indicates better flowability.
- Tapping tests evaluate the bulk density of the powder after successive drops or compression. A powder that compacts easily generally has better flowability.
- Rheological Studies measure the resistance to flow of the powder under different conditions of stress and deformation.
- Shear Cell Measurements evaluate flowability by applying a shear stress to the powder and measuring the force required to induce movement. This allows for a precise quantitative assessment of flowability.
Friability
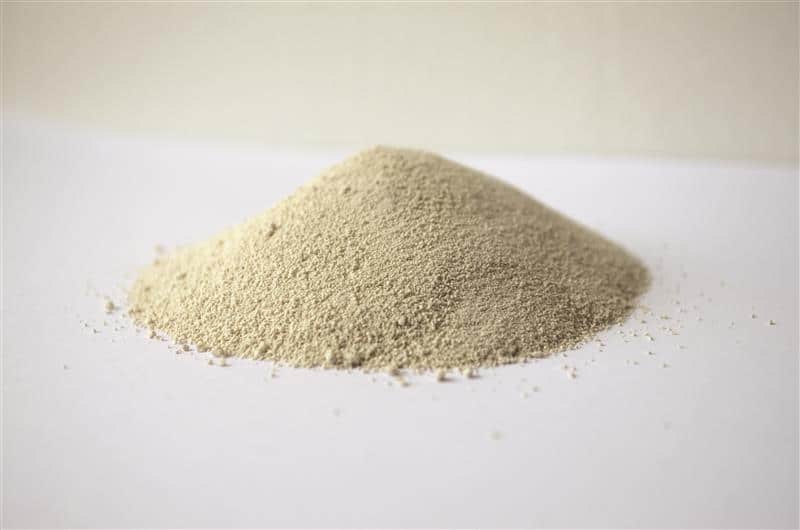
The friability is the degradation of granules by physical action (mechanical shocks, friction). It should be as low as possible so that it does not impact the quality of the product.
If the product is too friable, too much dust will be formed at the customer’s premises which can negatively impact the manufacturing, packaging, storage and transport. Products must be as resistant as possible during all those steps. Manufacturing, packaging, storage and transport themselves can also influence friability. It is also the case of the humidity content which can lead to lower friability if it is high.
Friability tests are widely used in the pharmaceutical industry to assess the physical strength and durability of tablets and uncoated products. The tool used for the friability measurement is called Friabilator or Friability Tester. Friability testers use a standardised, reproducible, reliable and effective method.
The friability is measured in percentage. The objective of Phosphea is to have a friability below 1%. Some products, such as MCP, have a friability closer to 0.5% which shows a good physical strength of the product.
pH
The pH of a phosphate should be taken into consideration according to the species concerned and the use of the final product. pH impacts enzyme activity and nutrients solubilization in stomach. Ruminants have a basic to neutral ruminal pH (6-7) while monogastrics have an acidic stomach pH (2-3). Feed formulators for pig and poultry are thus looking for low pH phosphate to protect the intestine from pathogens and promote the solubilization of nutrients. They even sometime use acidifier agents which help to maintain optimal pH in the stomach, allowing a correct function of the proteolytic enzymes and to control intestinal microflora.
Acidic pH can however be corrosive and thus strengthen the risk of premature wear on machines which is essential to keep in mind when switching from a basic to an acidic phosphate, particularly for mineral feed producers. Nevertheless, coating materials are often being used in animal feed factory lines which limit corrosive issue.
Each Phosphea’s inorganic feed phosphate has a fixed pH or specific pH range. The lowest pH value of Phosphea’s IFP is 3 and the highest pH value is 9.5.
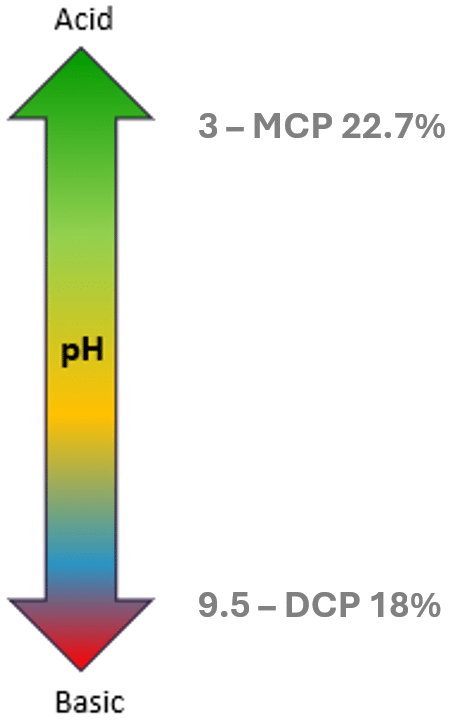
Phosphorus water solubility (Pws or Pse) and reactivity
Phosphorus water solubility (Pse) reflects the proportion of phosphorus (P) under MCP molecules, which are highly soluble in water. That’s why a MCP product has a Pse above 75% while a MDCP has a Pse above 65% and a DCP, whose P content comes mainly from DCP molecules, has a Pse below 10%. The quantity of MCP molecules of a product is highly and positively correlated with:
- its digestibility (for pig, poultry and aqua species) ;
- its availability for ruminal bacteria (for cows) ;
- its reactivity.
The reactivity of a product can be measured through the temperature rise at 5 minutes due to the reaction between phosphate and water. A reactive product will have an higher rise in temperature (exo-thermal reaction) which means a risk of chemical reaction with other components of the premix or mineral feed (ex : magnesium oxide).
Low to medium reactivity is therefore commonly sought for minerals, premix and lick blocks while high reactivity in compound feed or loose licks may not be a problem.
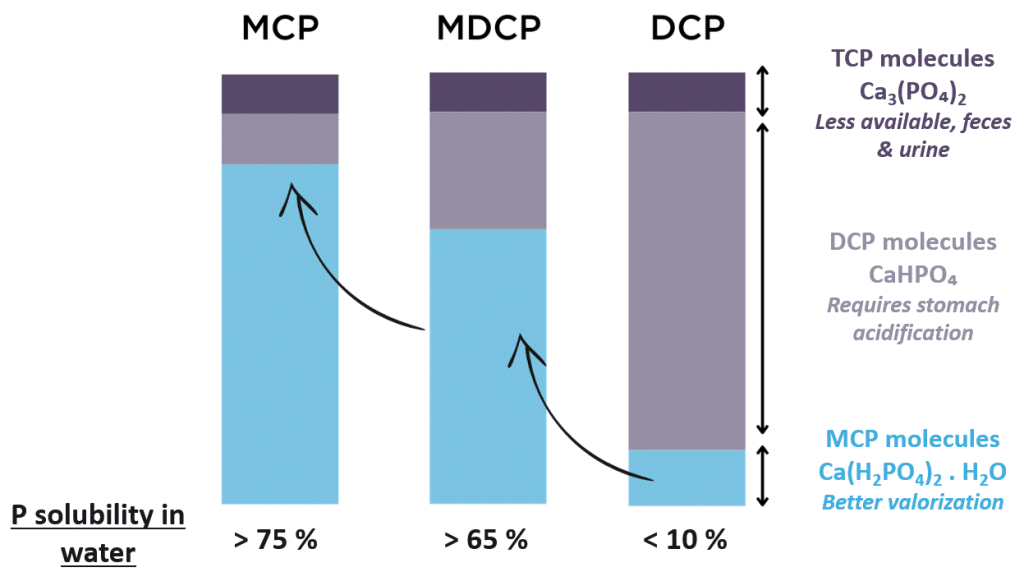
Free acidity and CO2
Free acidity reflects H3PO4 molecule content in the phosphate.
CO2 reflects CaCO3 molecules content in the phosphate.
In both cases, a too high value means that the reaction is not complete: P and Ca are not fully linked. The risk is higher for hygroscopic phosphates like MCP.
Free acidity and CO2 are used to control the production process.
Free acidity can increase caking risks.
Moisture absorption / Humidity
The humidity at 100% corresponds to the loss of free water. It should not exceed 2%. A high humidity increases the risk of chemical reactions, caking (reduced flowability) and bad storage.
The loss at 250°C or 550°C reflects water molecules linked with phosphates molecules.
The calculation Loss at 250°C or 550°C – Humidity at 100°C is used to know if a DCP is anhydrous or dihydrated. A result below 10% means that it is an anhydrous DCP whereas a result equal to or above 10% means that it is a dihydrated DCP which indeed will lose its linked water molecules and consequently more weight between 100°C and 250°C.
The humidity of a final product depends on the production process (drying method), the atmosphere/climate and the storage conditions.
Why is it very important to always analyze the % of humidity and the P content together ?
The higher the moisture content, the more phosphorus will be diluted in the product (for MCP for example that are very hygroscopic). The humidity content can thus impact the mass percentage of phosphorus in the product but the quantity of phosphorus in the product will always remain the same. The moisture content is also very important to take into consideration when measuring the heavy metals of a phosphate : the calculation should be done at 12% humidity.
The only EU regulation concerning the moisture content of phosphates concerns labelling : above 10% of moisture in the product, it must be stated on the label.